三聚氰胺作为一种重要的具有很好阻燃性能的精细化工基础有机原料,应用广泛。目前,三聚氰胺主要用于与甲醛缩合,生成三聚氰胺甲醛树脂(简称MF树脂)。该树脂不易着火,耐水、耐热、耐老化、耐电弧、耐化学腐蚀,有良好的绝缘性能、光泽度和机械强度,是木材、塑料、涂料、造纸、纺织、皮革、电器、医药、混凝土减水剂等工业不可缺少的化工原料。
①三聚氰胺的传统主要应用领域
资料来源:智研数据中心整理
②三聚氰胺潜在应用领域
随着三聚氰胺下游应用研发不断深入,以三聚氰胺为基础的新材料还可以应用于阻燃纤维、阻燃泡沫、聚氨酯阻燃剂、环保型清洁用品等行业。
资料来源:智研数据中心整理
三聚氰胺生产工艺概述
三聚氰胺生产工艺根据其所选用的原料不同,可以分为双氰胺法和尿素法。由于尿素为原料的生产工艺的各项技术经济指标远优于双氰胺为原料的工艺,双氰胺法已经被淘汰,目前世界上三聚氰胺生产工艺均为尿素法。
三聚氰胺尿素生产工艺主要分为高压法和低压法:高压法操作压力一般为8.0-15.0MPa,液相反应,不用催化剂;低压法操作压力一般为0.1-1.0MPa,气相反应,需要催化剂;低压法又分为常压法(0.3MPa 以下)和加压法(0.5-1.0MPa)。
根据三聚氰胺的分离工艺不同,生产工艺又可划分为液相淬冷法、气相淬冷法、固相淬冷法以及干捕再精制法。
三聚氰胺高压法和低压法的主要应用工艺及特点如下:
资料来源:智研数据中心整理
以尿素为原料生产三聚氰胺,无论是高压法或低压法生产三聚氰胺都由分解/聚合过程、淬冷过程、尾气处理三部分组成,具体如下:
资料来源:智研数据中心整理
我国早期主要开发了干捕再精制法工艺,后来在消化吸收国外先进技术的基础上开发了改良气相淬冷法。我国气相淬冷法以清华的改良气相淬冷法、北京烨晶加压气相淬冷法为代表。特别是北京烨晶加压气相淬冷工艺与BASF 工艺、清华改良气相淬冷工艺相比,其工艺流程、反应及分离单元关键设备、催化剂、尾气联产或分离技术都有重大改进和提升,装置可以长周期稳定运行,产能可以大型化,尾气处理和利用更经济合理和简单方便,能耗指标世界领先。目前,烨晶加压气相淬冷法已成为国内三聚氰胺生产的主流技术,又被称为“节能节资型气相淬冷法”工艺,也被我国业界称为“烨晶第三代气相淬冷技术”。
产业信息网发布的《2014-2019年中国三聚氰胺市场行情动态与发展前景预测报告》
20 世界80 年代,三聚氰胺主要生产工艺为高压法。随着低压法的不断改进,逐渐代替高压法成为三聚氰胺生产的主要应用工艺,高压法目前除欧技法还在使用外,其他工艺基本都已经淘汰。目前全球使用的三聚氰胺生产工艺情况见下图:
资料来源:智研数据中心整理
在全球主要的三聚氰胺生产工艺中,比较有竞争力的生产工艺主要为烨晶加压气相淬冷法、巴斯夫法、我国改良气相淬冷法。
(2)主要生产工艺特点
目前,世界范围内应用最广泛的三聚氰胺生产工艺主要技术指标比较如下:
备注:①未计入尿素和氨消耗的燃动力综合能耗值,能耗计算依据:GB/T50441-2007《石油化工设计能耗计算标准》,电力消耗按等价值折算。②两套日产100 吨装置联合布置。
烨晶加压气相淬冷法各项指标基本上都领先其他生产工艺,并且装置硬件投资最低,单套产能最大,综合能耗只有巴斯夫法和改良气相淬冷法的60%左右,欧技法的30%左右,在工业化生产中具有非常大的成本优势。
(3)三聚氰胺生产工艺发展趋势
近年来,三聚氰胺生产工艺向着生产规模大型化、投资最小化、资源利用最大化、环保节能等方向发展,生产规模小、综合能耗高的工艺将逐渐被淘汰。
目前在三聚氰胺尾气处理工艺主要有:尾气送尿素、硫铵、硝酸铵或碳酸氢铵生产装置进行联产;采用氨碳分离技术将尾气分离成纯氨和二氧化碳。不同的三聚氰胺尾气处理工艺特点如下表:
资料来源:智研数据中心整理
联产尿素、硫铵、硝酸铵或碳酸氢铵是一个将尾气作原料与下游产品装置联合生产的过程,需要上游三胺装置与下游产品装置间高度的生产协同。在整个连续生产的循环过程中,三聚氰胺装置停车或联产装置停车都将影响整个联产过程的运行。
氨碳分离技术将三聚氰胺尾气分离成纯氨(可储存)和纯二氧化碳后再用于生产尿素或其他产品,也可作为产品直接销售。氨碳分离工艺纳入三聚氰胺装置一体化设计建设生产运行,下游产品装置生产相对独立,应对市场具有更强的灵活性。


2025-2031年中国三聚氰胺行业市场深度分析及投资前景展望报告
《2025-2031年中国三聚氰胺行业市场深度分析及投资前景展望报告》共十九章,包含三聚氰胺产业投资风险,三聚氰胺合成工艺,三聚氰胺的投资预算等内容。
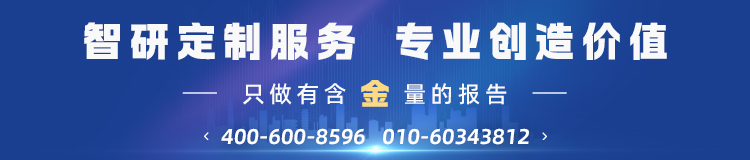
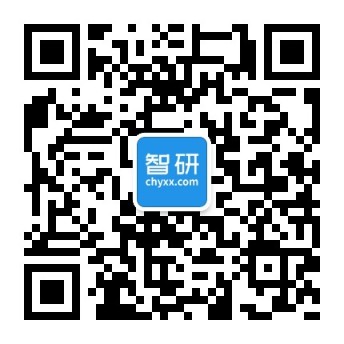
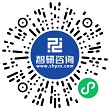
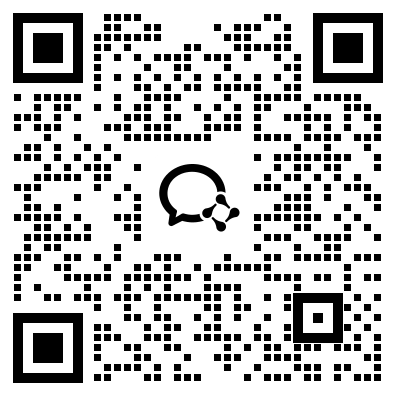